Spray Polyurethane Foam Roofing, or spray foam roofing, is a material that’s sprayed as a liquid so it can expand into a foam, creating a solid layer across an existing roof.
Roof Repair in Los Angeles's usual application of spray foam is to repair and reinvigorate an existing roof by removing the saturated areas, replacing them with like materials, and then spraying foam over top of the entire roof.
While SPF roofing is not the most known type of roofing material, the technology has been around since the early 1960s for industrial, commercial, and residential facilities. An SPF roofing system can be used in any climate, and when correctly installed and maintained, can last over 50 years.
Spray Polyurethane Foam (SPF) for roofing applications is manufactured on the job site by mixing two highly reactive chemicals.
The chemicals, A (polyol/resin) & B (isocyanate), are pumped from separate containers through heated, high-pressure hoses to an internal mixing spray gun.
Many changes have occurred in the equipment and chemistry of polyurethane roofing in the last fifty years, resulting in today’s dependable roof applications.
What Are The Advantages Of A Spray Polyurethane Foam Roof?
1. Spray Foam Roofs Have A High R-value
- Spray polyurethane foam has the highest R-value of any commonly used roof insulation. Here are the average R-values for some common roof materials
- Spray Polyurethane Foam: 6.6 per inch
- Metal: 0.00 per inch
- BUR Gravel: 0.34 per inch
- BUR Smooth: 0.24 per inch
- XPS Insulation: 5.0 per inch
- EPS Insulation: 3.85 per inch
- Polyiso: 5.5 per inch
- R-value is the capacity of an insulating material to resist heat flow. The higher the R-value, the greater the insulating power
- The higher the R-value, the less heat or cool air will pass through. Higher R-value = less HVAC use = lower energy costs
- Total payback of your new roof usually occurs in less than ten years through savings in heating and cooling costs.
2. Spray Foam Roofs Are Renewable
- One of the benefits of a polyurethane roof is its ability to be re-coated.
- A properly installed and maintained spray polyurethane foam roof should not require re-coating for 10 to 20 years. The best way to determine when a spray foam roof needs to be re-coated is to measure the remaining coating thickness on the roof and recoat before the coating is too thin to provide U.V. protection.
- The first application of the coating is usually applied at a thickness of 20-30 mils.
- After 10 years, the coating could be reduced to a thickness of 7-10 mils, depending on the wear of the roof.
- Many coating manufacturers offer extended warranties with each re-coat. This option, along with scheduled maintenance, allows a spray foam roof to be a truly renewable roof system.
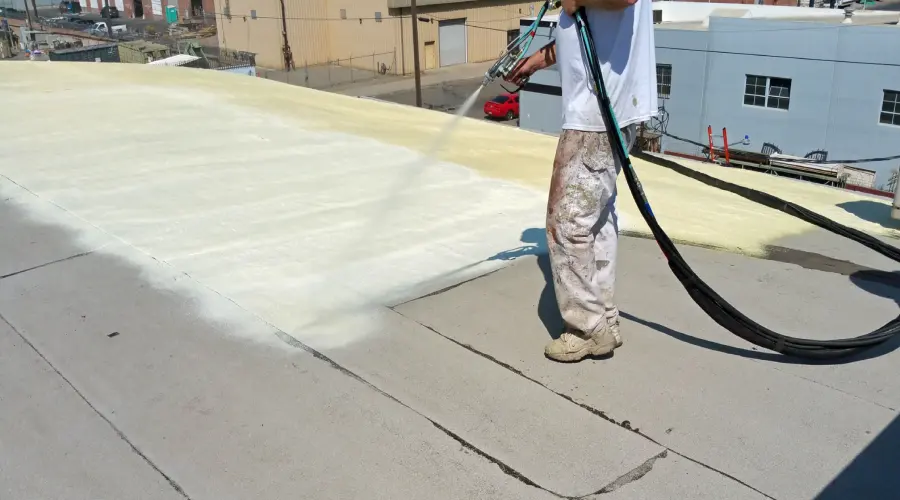
Spray Polyurethane Foam Roofs Are Quickly Installed
- Spray foam roofs are installed quicker than other roofing systems, due to:
- Most SPF roofing projects involve little to no tear-off
- Spray foam roofs are spray-applied, meaning they can go around penetrations with ease
- Spray foam roofs require less material and equipment than traditional roofing systems
- One example would be roofing around a penetration. With spray foam being “spray-applied”, it would take about 2 minutes to roof around a penetration, as opposed to rubber roofing, which can take at least 30 minutes due to the custom cutting of materials.
Spray Polyurethane Foam Roofs Are Self-flashing
Self-flashing refers to spray foam’s ability to conform to irregular shapes. Watch the video below which shows spray foam being sprayed around a curb:
In the video, it says it might take a conventional roofer 30 minutes to flash around a curb, and spray foam can be applied in about two minutes.
Other roofing systems, like rubber, will need to be custom-cut to be installed properly around a curb.
Self-flashing allows spray foam to be applied faster around all penetrations, including:
- Parapet walls
- Vents
- Pipes
- HVAC units
- Skylights
- Drains
Spray Polyurethane Foam Is Seamless
A big advantage spray polyurethane foam has over other roofing systems is that it’s seamless.
Being seamless, and therefore monolithic and watertight, avoids traditional single-ply membrane seams that tend to be the sources of leaks.
Seam separation of a rubber roof. An invitation for water penetration that will cause a roof leak.
How Do Leaks Form On A Rubber Roof?
Seams start to separate over time and allow water to get inside. Also, they can allow some water to get in, it freezes, and when it thaws out, it breaks apart the seam even more.
Wind uplift is also an issue with seams. Wind will eventually get underneath a slightly separated seam, loosen and eventually allow an opportunity for water to enter the building.
With spray foam being seamless, there is no opportunity for wind to get underneath a spray foam roof.
How Much Does A Spray Foam Roof Cost?
The cost of materials changes daily. On average, a spray foam roof costs between $8 – $12 per square foot. Two years ago (2020), the cost was $4-$7 per square foot. There’s a lot of volatility in material prices today (October 2022).
Here are other reasons why the price can go up or down, such as:
Location
The further away you are from a spray foam roofing contractor, the more expensive the project will be.
It will be more cost-effective if you’re close to a roofing contractor.
What Problems Do Spray Foam Roofs Have?
There are three problems with spray foam roofs, they are:
Bad/Inexperienced Contractors Installing Foam
It’s sad to say, but there are some terrible spray foam
Roof Contractors. These contractors aren’t experienced in spraying foam. They are using each roofing project they get as an opportunity to “see” if they can spray good foam.
There are many ways to tell a good spray foam roofing contractor vs. a bad one, but the first one is to show proof that you are certified with the SPFA. (Spray Polyurethane Foam Association)
One SPFA certification includes applicators spraying over 500,000 sq. ft. of foam.
Needs To Be At Least 50 Degrees To Apply
The temperature needs to be at least 50 degrees to apply spray foam. If you install spray foam in too cold of weather, the reaction of the two chemicals will be off, and the foam will not perform how it was designed to.
Overspray
Since the foam is very light, it can be carried away by the wind. To combat overspray, roofing contractors must cover nearby cars, use windshields, or spray out of an enclosed booth.
If foam lands on an area it wasn’t supposed to, it can be removed with car detailing. This is done by using a clay bar or letting the foam degrade on its own with exposure to UV rays.
What Roofing Systems Can Spray Foam Be Applied To?
Some commercial roofing systems can handle spray foam, and some need some tweaking before spray foam can be applied. Let’s take a look:
Metal Roof
- Spray foam can be installed right over a metal roof.
- A rust inhibitor primer may be needed to stop oxidation if some of the metal is currently rusted.
- One benefit of spray foam for metal roofs is that metal roofs have crimped panels, which leave tiny holes for water and air to enter/exit your building.
- Applying spray foam makes your roof one continuous layer, covering these exposed areas.
TPO
- Spray foam can be installed over a TPO roof if a cover board is installed first over the existing TPO.
- It doesn’t matter if the existing TPO roof is fully-adhered or mechanically attached; a cover board is always needed when installing spray foam over TPO.
- TPO is slippery, so a cover board is needed to have the best possible adhesion.
EPDM
Spray foam can be applied to any of the three types of EPDM roofs: fully adhered, mechanically fastened, or ballasted.
For a fully-adhered EPDM roof, spray foam can be installed right over the top, as long as the EPDM is aged (more than 5 years old).
For a mechanically-fastened EPDM roof, a cover board will need to be installed first, then the spray foam can be installed over the top.
The rocks will need to be removed first for a ballasted EPDM roof. A cover board will need to be installed (because nothing is holding that EPDM down once the rocks are removed), and then spray foam can be installed over the top.
Built-Up Roofs
Spray foam can be installed on a smooth or gravel-surfaced built-up roof since the roof is fully-adhered to the underlying substrate.
For spray foam to be installed over a gravel built-up roof, a wet-vac process must remove the stones and gravel so there’s a clean surface left behind.
Modified Bitumen
Spray foam can be installed over an existing modified bitumen roof. Since “mod-bit” comes in a roll, whether they are torched or adhered down, it’s a fully-adhered system where a cover board isn’t needed.
Now that we know how each roofing system can handle a spray foam installation, let’s get into the benefits the system provides.